How to Calculate Throat Size and Leg Length in a Fillet Weld
Fillet welds are the unsung heroes of structural engineering, providing strength and versatility in everything from bridges to pressure vessels. Whether you’re a welder, engineer, or inspector, understanding how to calculate throat size and leg length in a fillet weld is critical to ensuring weld quality, structural integrity, and compliance with industry standards. These dimensions directly influence a weld’s load-carrying capacity and durability, and getting them wrong can lead to costly failures or safety risks.
In this blog post, we’ll dive deep into the definitions, calculations, and practical examples of throat size and leg length, referencing key codes like AWS D1.1, ASME BPVC Section IX, ISO 5817, and AS/NZS 1554, to deliver a clear, accurate, and actionable guide.
What Are Throat Size and Leg Length?
Before we crunch numbers, let’s clarify the terms:
- Leg Length: The distance from the root of the fillet weld (where the weld meets the base metal intersection) to the outer edge of the weld along each of the two base metal surfaces. In an equal-leg fillet weld, both legs are of the same length. Leg length is typically specified in drawings (e.g., 6 mm) and is the primary dimension welders aim to achieve.
- Throat Size: The shortest distance from the root of the weld to the hypothetical face of the weld (the outer surface if it were perfectly flat). For a right-angled fillet weld, the theoretical throat is the perpendicular distance, while the effective throat includes penetration into the root. Throat size determines the weld’s strength, as it governs the cross-sectional area resisting shear or tensile forces.
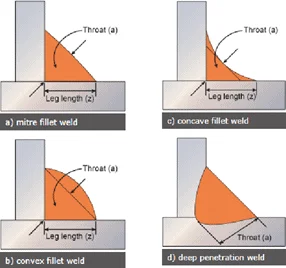
These dimensions are interrelated, and standards like AWS D1.1:2020 and AS/NZS 1554.1:2014 provide guidelines for measuring and calculating them to ensure welds meet design requirements.
Why Calculating Throat Size and Leg Length Matters
Fillet welds are designed to transfer loads between connected components, and their strength depends on the throat size, which defines the effective area resisting forces. Incorrect sizing can lead to:
- Underwelding: A throat too small reduces strength, risking failure under load.
- Overwelding: Excessive leg length wastes material, increases costs, and may cause distortion.
- Non-Compliance: Failing to meet code requirements (e.g., ASME or ISO) can result in rejected welds or project delays.
For example, in a steel bridge, undersized fillet welds might crack under cyclic loading, while oversized welds in a pressure vessel could introduce unnecessary heat, warping the material. Accurate calculations ensure safety, efficiency, and compliance.
Key Codes and Standards
Several codes provide guidance on fillet weld dimensions, calculations, and tolerances. Here’s a summary of relevant standards:
Standard | Reference Section | Key Guidance |
---|---|---|
AWS D1.1:2020 | Figure 4.1 | Defines leg length as the design dimension; throat size as 0.7 × leg for equal-leg welds; specifies inspection tolerances. |
ASME BPVC Section IX:2023 | QW-452.5 | Focuses on qualification; throat size critical for procedure qualification; leg length measured for visual acceptance. |
ISO 5817:2023 | Table 1 | Specifies quality levels (B, C, D); throat size (effective) must meet minimum design values; leg length tolerances defined. |
AS/NZS 1554.1:2014 | Clause 3.3 | Requires leg length to match specified size; throat size calculated as 0.7 × leg for 45° fillet welds; emphasizes effective throat for strength. |
EN 1011-2:2001 | B.3 | Recommends throat size as primary strength parameter; leg length secondary for inspection purposes. |
These standards emphasize that throat size is the primary determinant of weld strength, while leg length is a practical measure for welders and inspectors.
Understanding Fillet Weld Geometry
A fillet weld typically forms a right-angled triangle in cross-section, with two legs and a hypotenuse (the weld face). The geometry varies based on the weld type:
- Equal-Leg Fillet Weld: Both legs are equal (e.g., 6 mm × 6 mm), forming a 45° angle at the root.
- Unequal-Leg Fillet Weld: Legs differ (e.g., 6 mm × 8 mm), altering the throat calculation.
- Concave Weld: The weld face curves inward, reducing the effective throat.
- Convex Weld: The weld face bulges outward, potentially increasing throat but complicating inspection.
The theoretical throat assumes a flat weld face, while the effective throat accounts for penetration or concavity, as defined in AWS D1.1 Clause 2.4.2.3.
Calculating Throat Size and Leg Length
Let’s break down the calculations for throat size and leg length, focusing on equal-leg fillet welds, as they’re the most common. We’ll also cover unequal-leg cases and practical considerations.
1. Theoretical Throat Size
For an equal-leg fillet weld with a 45° angle (isosceles triangle):
Throat Size (a) = Leg Length (z)/ sin (45)
Since sin(45) approx 0.707, the formula simplifies to:
a = z x times 0.707
Example:
- Leg Length: 8 mm
- Calculation: a = 8 x times 0.707; approx. 5.66 mm
- Result: Theoretical throat size is 5.66 mm.
For unequal-leg fillet welds, the throat size is the shortest distance from the root to the weld face, calculated using trigonometry or CAD tools. A simplified approach uses the smaller leg:
- a approx. Smaller Leg x times 0.707
Example:
- Legs: 6 mm (vertical), 10 mm (horizontal)
- Calculation: a approx. = 6 x times 0.707 =approx. 4.24mm
- Note: Exact throat requires geometric analysis, as per ISO 5817 Annex A.
2. Effective Throat Size
The effective throat includes root penetration (for partial penetration welds) or accounts for concavity/convexity. Per AWS D1.1:
- Effective Throat = Theoretical Throat + Weld Penetration
For concave welds, the throat may be reduced:
- Effective Throat= Distance from Root to Lowest Point of Weld Face
Example:
- Leg Length: 8 mm
- Theoretical Throat: 5.66 mm
- Penetration: 1 mm (measured via macro-etch)
- Calculation: Effective Throat = 5.66 + 1 = 6.66 mm
3. Leg Length from Throat Size
If the design specifies throat size (common in EN 1011-2), you can calculate the required leg length:
a ≈ 0.7z and z ≈ 1.4 a
(For the maths-minded, 0.7 is 1/√2 and 1.4 is √2).
Example:
- Required Throat: 5 mm
- Calculation: z = 1.4 x 5
- Result: Leg length of approximately 7 mm is needed.
4. Weld Size Tolerances
Standards specify tolerances to ensure welds meet design intent:
- AWS D1.1: Leg length ±1/16 inch (1.6 mm); throat size must not be less than specified.
- AS/NZS 1554.1: Leg length ±1 mm; throat size ≥ 0.7 × specified leg.
- ISO 5817 Level B: Throat size deviation ≤ -0.3 mm for stringent applications.
Practical Examples
Let’s apply these calculations to real-world scenarios, aligning with code requirements.
Example 1: Structural Steel Beam (AWS D1.1)
- Project: Welding a steel beam (ASTM A36) to a column.
- Design: Fillet weld with 6 mm leg length, equal legs.
- Process: SMAW with E7018 electrode.
- Calculation:
- Throat Size: a = 6 x times 0.707 = approx. 4.24 mm
- Strength Check (per AWS D1.1 Clause 2.4.2.9):
- Shear capacity ∝ throat size × weld length.
- For E7018 (70 ksi), allowable shear stress ≈ 21 ksi.
- Effective throat = 4.24 mm; capacity sufficient for design load.
- Inspection: Measure leg length with a fillet weld gauge; ensure throat ≥ 4 mm.
- Result: Weld meets AWS D1.1; visual and dimensional checks pass.
Example 2: Pressure Vessel Weld (ASME BPVC IX)
- Project: Fillet weld on a nozzle-to-shell joint (SA-516 Gr. 70).
- Design: 8 mm throat size specified.
- Process: GTAW with ER70S-2 filler.
- Calculation:
- Leg Length: z = 8/07.707 = approx. 11.32 mm
- Rounded: Use 12 mm leg length for practicality.
- Recalculate Throat: a = 12 x times 0.707= approx. 8.48mm
- Qualification: Per ASME QW-452.3, welder qualifies for 8–10 mm throat; procedure tested via macro-etch.
- Result: Weld exceeds minimum throat, ensuring strength; complies with ASME IX.
Example 3: Unequal-Leg Weld (AS/NZS 1554.1)
- Project: Crane rail to steel plate.
- Design: Unequal-leg fillet weld (5 mm vertical, 8 mm horizontal).
- Process: FCAW with E71T-1.
- Calculation:
- Approximate throat: a = 5 x times 0.707 = approx. 3.54 mm
- Exact throat (geometric):
- Use Pythagorean theorem for hypotenuse; throat = shortest perpendicular distance.
- CAD or formula: a = approx. 3.6 mm (simplified for blog).
- Check: AS/NZS 1554.1 requires throat ≥ 3.5 mm; weld passes.
- Result: Weld meets load requirements; leg lengths verified with gauge.
Measuring Throat Size and Leg Length
Accurate measurement is as crucial as calculation. Common methods include:
- Fillet Weld Gauge: Measures leg length directly; AWS D1.1 recommends for visual inspection.
- Macro-Etch Testing: Cuts weld cross-section to measure throat and penetration (ASME IX requirement for qualification).
- Ultrasonic Testing (UT): Estimates throat size non-destructively, per ISO 5817 for high-quality welds.
- Laser Profilometry: Advanced method for precise geometry, used in research or critical applications.
Note: Convex welds may overestimate throat size visually; concave welds require effective throat measurement to avoid underestimating strength.
Common Pitfalls and How to Avoid Them
- Assuming Equal Legs: Always check drawings; unequal legs require adjusted calculations.
- Ignoring Penetration: Effective throat includes root penetration, critical for partial penetration welds (AWS D1.1).
- Overlooking Concavity: Concave welds reduce throat size; adjust leg length to compensate (ISO 5817).
- Neglecting Tolerances: Exceeding leg length tolerances wastes material; stay within code limits (AS/NZS 1554).
- Misinterpreting Standards: ASME focuses on throat for strength, while AWS emphasizes leg for inspection—know your code.
Practical Tips for Welders and Engineers
- Read Drawings Carefully: Confirm leg length or throat size requirements; note equal vs. unequal legs.
- Use Weld Imperfection Charts: AS/NZS 1554.1 Annex C helps identify acceptable concavity/convexity.
- Calibrate Gauges: Ensure fillet weld gauges are accurate for consistent measurements.
- Document Measurements: Record leg and throat sizes for traceability, especially for ASME or ISO projects.
- Consult Standards: Cross-reference AWS, ASME, or ISO for project-specific rules.
- Test Critical Welds: Use macro-etch or UT for high-stakes applications like pressure vessels.
Summary Table: Throat Size and Leg Length Relationships
Weld Type | Leg Length (z) | Throat Size (a) | Formula | Notes |
---|---|---|---|---|
Equal-Leg, Flat Face | 6 mm | 4.24 mm | a = z x times 0.707 | AWS D1.1 standard assumption. |
Equal-Leg, Concave | 6 mm | < 4.24 mm | Measure to lowest point | ISO 5817 requires compensation. |
Unequal-Leg (5 × 8 mm) | 5 mm (min) | ~3.6 mm | Approximate: a= Smaller Leg x times 0.707 | Exact requires CAD or trigonometry. |
Effective Throat | 6 mm + 1 mm penetration | 5.24 mm | a = (z x times 0.707) + Penetration | ASME IX for qualification. |
Conclusion
Calculating throat size and leg length in a fillet weld is a blend of geometry, engineering, and code compliance. By understanding the relationship between these dimensions—throat as the strength driver, leg as the measurable target—you can design and execute welds that are safe, efficient, and compliant. Whether guided by AWS D1.1 for structural steel, ASME BPVC IX for pressure vessels, ISO 5817 for quality levels, or AS/NZS 1554 for Australian projects, accurate calculations prevent under- or overwelding, saving time and resources. Use fillet weld gauges, verify with testing, and always align with your project’s standard to ensure success.
Got a weld sizing question? Share your project details in the comments, and let’s crunch the numbers together!
References
- AWS D1.1/D1.1M:2020, Structural Welding Code – Steel, American Welding Society.
- ASME Boiler and Pressure Vessel Code, Section IX:2023, Welding and Brazing Qualifications.
- ISO 5817:2023, Welding – Fusion-welded joints in steel, nickel, titanium and their alloys – Quality levels for imperfections.
- AS/NZS 1554.1:2014, Structural steel welding – Welding of steel structures.
- EN 1011-2:2001, Welding – Recommendations for welding of metallic materials – Arc welding of ferritic steels.